- Examples Of Quality Objectives Manufacturing
- Quality Objectives Examples Manufacturing Companies
- Manufacturing Quality Objectives Examples Pdf
- Quality Objectives Examples Manufacturing Company
Cost of quality (COQ) is defined as a methodology that allows an organization to determine the extent to which its resources are used for activities that prevent poor quality, that appraise the quality of the organization’s products or services, and that result from internal and external failures. Having such information allows an organization to determine the potential savings to be gained by implementing process improvements.
What is Cost of Poor Quality (COPQ)?
Definition of success relative to Quality Objectives. Ensure customer endorsement of all quality objectives included in the Quality Management Plan. Do Do the work according to the approved PMP and standard operating procedures. Project execution is a dynamic process. The PDT must communicate, meet on a regular basis, and adapt to changing. Companies must link manufacturing objectives to their strategic business objectives. His secret obsession pdf free. Manufacturing objectives such as improving quality, reducing costs, speeding throughput and increasing production flexibility help companies compete more effectively and meet their customers’ price, quality and delivery requirements. Example Objectives (second set) Make our company profitable on a long-term basis. Develop additional market opportunities. Quality objectives are quality control goals that a company sets according to ISO 9001:2015 standards. These goals have to be SMART so that the employees could have a complete understanding of how and what they should to boost their organisational efficiency. The abbreviation stands for: Specific. The item for improvement has to be clearly defined. Quality objectives vary greatly depending on the industry, company, product, or service. Here are a few general examples: Increase total sales by 10% from Q1 to Q2 Decrease failed customer resolutions by 20% by the end of the month.
Cost of poor quality (COPQ) is defined as the costs associated with providing poor quality products or services. There are three categories:
- Appraisal costs are costs incurred to determine the degree of conformance to quality requirements.
- Internal failure costs are costs associated with defects found before the customer receives the product or service.
- External failure costs are costs associated with defects found after the customer receives the product or service.
Examples Of Quality Objectives Manufacturing
Quality-related activities that incur costs may be divided into prevention costs, appraisal costs, and internal and external failure costs.
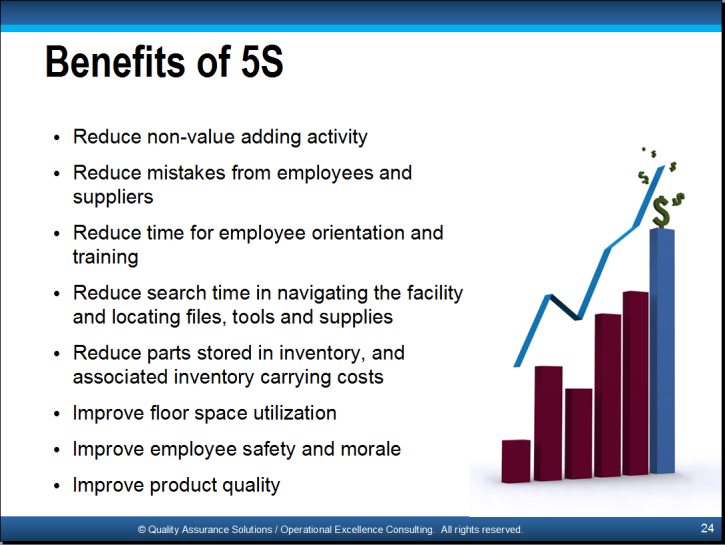

Appraisal costs
Quality Objectives Examples Manufacturing Companies
Appraisal costs are associated with measuring and monitoring activities related to quality. Bamini tamil typing practice book. These costs are associated with the suppliers’ and customers’ evaluation of purchased materials, processes, products, and services to ensure that they conform to specifications. They could include:
Manufacturing Quality Objectives Examples Pdf
Quality Objectives Examples Manufacturing Company
- Verification: Checking of incoming material, process setup, and products against agreed specifications
- Quality audits: Confirmation that the quality system is functioning correctly
- Supplier rating: Assessment and approval of suppliers of products and services
Comments are closed.